CONTENTS
What is the best way to use solid wood from the Kii Peninsula?
Great color. Lustrous. Outstanding toughness. Excellent strength and durability. Tightly-packed growth rings. Straight grain. These are the words people use to describe wood from Wakayama known as Kishuzai, or Kishu wood. Forests cover roughly 77% of Wakayama Prefecture—formerly known as Kishu—which explains why it has long been called the Kingdom of Trees. A silviculture technique distinct to Kishu has been developed over the years: the counterintuitive practice of higher-density planting in the mountain forests to delay growth. Rather than growing large trees as quickly as possible, Kishu growers take deliberate steps to create wood with a healthy gleam. This careful procedure of growing the right trees in the right places produces outstanding Kishu wood.
Yamacho Co., Ltd. was founded in the 18th century. The company is one of Japan’s largest holders of forest land, with 6,000 ha (more than 10,000 football fields) mainly in the southern part of the Kii Peninsula. It stands out even among Japanese companies for its integrated system that covers everything from planting to logging, lumbering, drying, milling, quality inspections, classification, and pre-cutting. Yamacho expanded into the silviculture business in the mid-19th century as a wholesaler of charcoal and forest products, and since then has continued to protect and cultivate the forests that eventually become Kishu wood based on the concept that one generation plants a forest, the next tends it, and the next converts it to wood and delivers it to society.
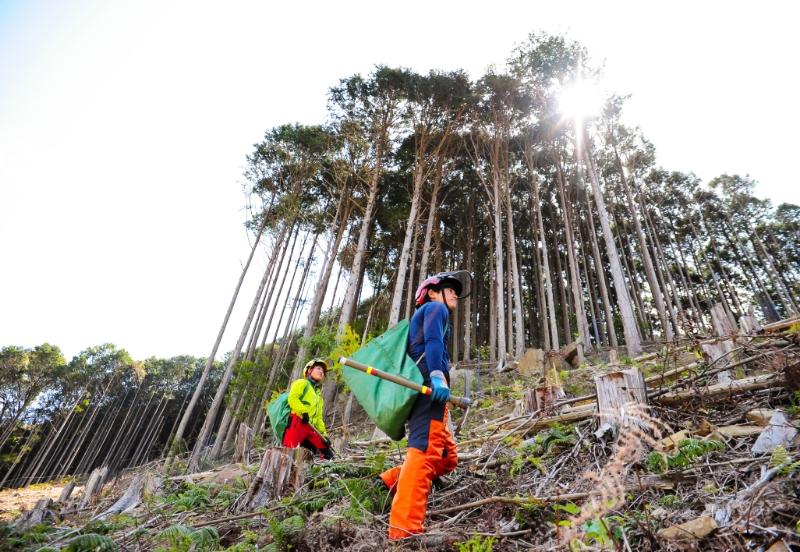
Growing seedlings: The first step of Yamacho silviculture
Kishu wood is regarded for its quality, which is as high as any world-class conifer wood. It is extremely workable, and the durability of the heartwood is excellent. Of course, the quality of solid wood as structural material is difficult to discern because its distinctive traits are not uniform or consistent. Yamacho undertakes various efforts to work around this issue, and ultimately to raise the value of Kishu wood.
High quality: The result of our integrated production system
“Our greatest strength at Yamacho is our ability to identify the very best wood,” Planning Department Manager, Director, and Corporate Planning Office member Takashi Sakohira said. In this business, the producers are visible in all aspects from planting to logging. The company knows where the best wood grows, and rewards customers’ trust in this knowledge with high-quality wood. “Like people, every tree is unique,” Sakohira said. “Some grow tall and straight, while others bend and twist. Thus, the judgment of our seasoned professionals and their knowledge of how the trees grow is needed to select the best wood in the lumbering and fabricating processes. Our integrated production system is what allows us to take advantage of this judgment at every step to supply high-quality wood.”
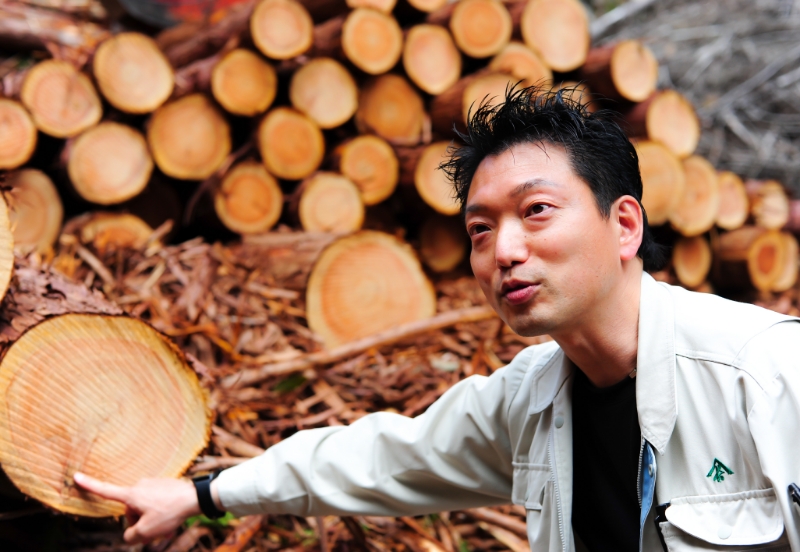
Takashi Sakohira, Planning Department Manager, Director, and Corporate Planning Office member at Yamacho
First and foremost, in the lumbering process, professionals carefully inspect logs for peculiarities before sawing them. Advanced techniques are required to overcome the extreme difficulty of processing logs into straight lumber. Our seasoned professionals take as much time as they need to saw logs for decorative beams, central pillars, and other wood longer than 6 m, all of which tend to have bends and twists. Although many of the processes involve a multitude of special requests from builders, these are opportunities for us at Yamacho to demonstrate our skills. This is why we treasure our professionals’ technical skills and exacting attention to detail.
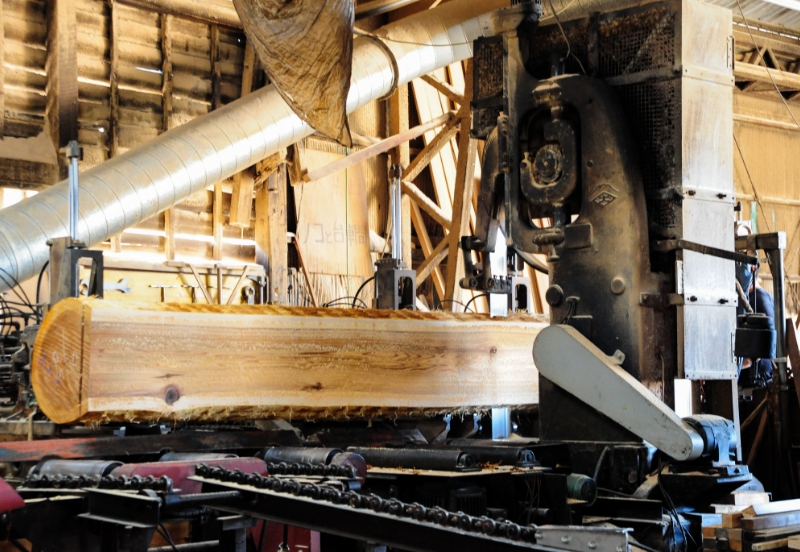
At the sawmill, logs are separated by size (3 m, 4 m, 6 m or longer) for lumbering
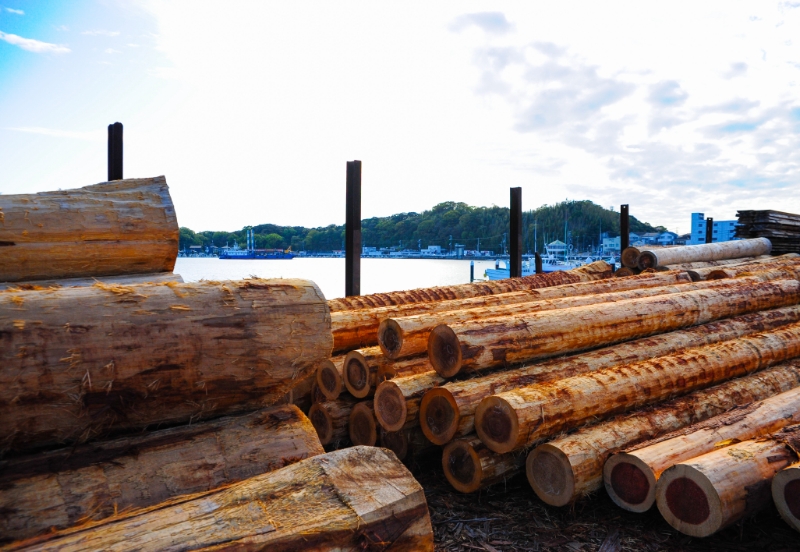
Logs with bark stripped off, ready to be transported from the timber yard to the sawmill
After lumbering, the enhanced drying process awaits. If logs are simply left out to dry, they will shrink, causing surface cracking and warping. Our proactive adoption of superheated steam vacuum dryers and other enhanced drying equipment enables us to control temperature and drying time and ultimately to dry logs at lower temperatures than conventional methods. Now that we can limit discoloration, burnt odors, internal cracking, and other problems with the wood, we have established the foundation for solid wood to serve different purposes reliably.
In 2008, the company became the first in Japan to acquire JAS certification for and manufacture flat-square cedar lumber. “Our achievement of JAS certification by virtue of rigorous mechanical measurement of strength and moisture content is proof that the quality of our solid wood is as high and consistent as commonly used laminated wood,” Sakohira said. “Our decorative beams, which reduce discoloration and better showcase natural colors, enrich architecture and living spaces.”
Our integrated production system originating in the wilderness enables us to manufacture, supply, and circulate consistently outstanding Japanese wood, and is highly regarded—it earned a Good Design Award in 2013 and the Emperor’s Cup at the 60th Agriculture, Forestry and Fisheries Festival in 2021. We continue to steadily earn trust with our unwavering involvement in all processes from forest management to logging, lumbering, and drying.
Looking into every invisible detail
We want to increase demand for homes made of solid wood. We want to make it easier for people to choose high-quality Kishu wood. These desires drove us to establish our pre-cutting plant for fabricating domestic solid wood in 1997. The plant is where we process and prepare the components of entire houses before selling them to the builders who assemble them. We examine the properties of each and every piece of solid wood and carefully consider the best way to use it, and then our specialists create the CAD data used in our fully automated cutting process. Finally, we painstakingly inspect the fabricated wood for imperfections and flaws before shipping them to the builders.
Traditionally, when someone wanted to build a wooden house, they would hire a carpenter to purchase solid wood, examine it, and use it where appropriate. Although all industries are struggling with labor shortages of late, the housing sector is also facing a dearth of carpenters capable of working with solid structural materials. “The solid wood we handle at our pre-cutting plant may look perfectly square once we cut it into pillars and beams, but even those pieces contain peculiarities from growing in the wild, so we must rely on the judgment of our seasoned professionals,” Sakohira said. The company deals directly with designers and builders, and thus is able to source wood while discussing matters and exchanging drawings with carpenters. “This facilitates our delivery of the right wood not only for conventional housing, but also for major undertakings and complicated projects.”
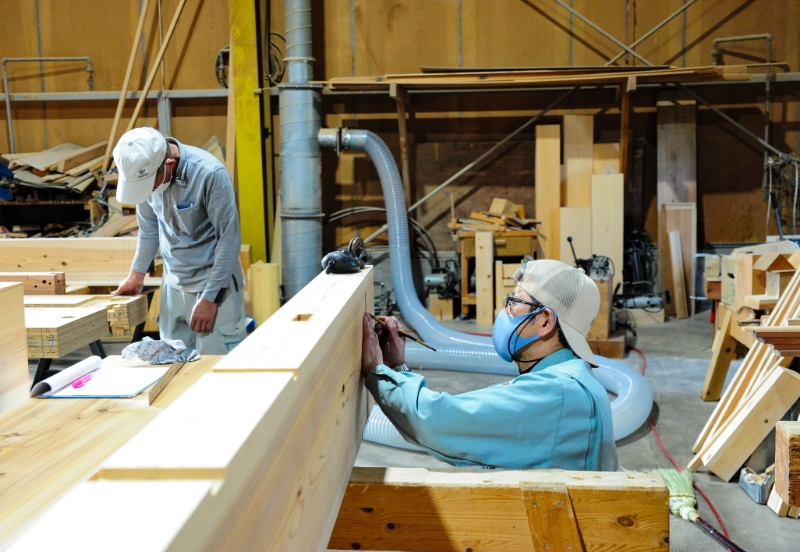
Our skilled professionals perform final checks without fail at our pre-cutting plant
Capitalizing on the skills of our technicians in the fabrication process has made assembling houses like model building—no special skills are needed to build houses that exhibit the best properties of high-quality solid wood. Houses made of natural wood—from the structural, interior, and other building materials to the walls, floors, and ceilings—have fewer problems such as sick building syndrome. Pillars, beams, and interior components made of wood absorb and release moisture, which has the effect of regulating indoor humidity. “Houses are like people—their pillars and beams correspond to our bones,” Sakohira said. “Those are arguably the most important parts, even though they cannot be seen. This is why we want to spread the word about the value of houses made of solid Kishu wood.”
The essence of forestry is maintaining the cycle of forest resources
Yamacho actively collaborates not only with group companies, but also with local companies involved in silviculture, logging, and similar endeavors. We interact often with other companies engaged in caring for trees as they grow, and also intend to focus on improving awareness of forestry amid an increasing desire to promote forestry education in Wakayama. In recent years, we have also proactively collaborated with companies and designers in other industries, for example with Takeshi Sawada (kamina&C) on Yatagarasu Stool, and incorporating Mino ceramic ware technology into UFUFU, an egg tile bath mat. The aim behind all of these efforts is to increase wood consumption by giving people as many opportunities as possible to encounter domestically grown and processed wood.
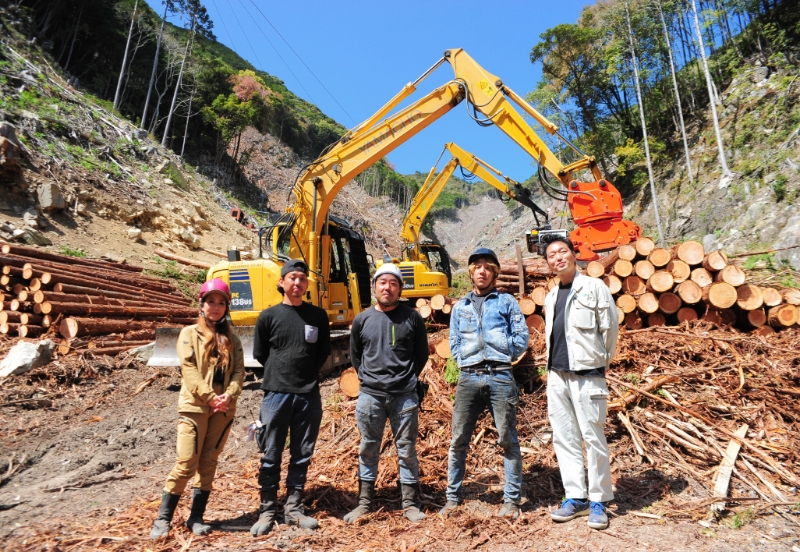
Logging (“harvesting”) in collaboration with a local company
Sakohira spoke to the significance of maintaining forests. “Forestry is an expanded version of farming—the act of cutting down trees is akin to harvesting,” he said. “Trees need to grow for 50 to 60 years before they are ready to become Kishu wood, so any trees I plant will be harvested by my children’s or grandchildren’s generation. In that sense, forestry works on a longer timespan than farming and is established across multiple generations.”
Trees absorb carbon dioxide from the air and create oxygen. However, their absorption rates decline as they age. At 50 to 60 years of age, trees are cut down, and new ones are planted to replace them. The act of planting, tending, cutting down, and planting again constitutes a cycle and promotes the circulation of the atmosphere. Indeed, cutting down trees to use their wood is an integral part of conserving nature.
Plant, tend, harvest.
The essence of forestry is to continually renew trees that produce decades of oxygen.
Yamacho has contributed to forestry in Japan with an integrated system in which we manage natural materials from planting and tending to homebuilding. We will maintain our quiet focus on the future of manufacturing: circulating Japan’s forest resources.