Re-examining Japan’s Trees
for Application in Daily Life
2021.12.21
Aiming for New Styles of Craftsmanship Through Shoji Screens
The scent of freshly cut trees emanates from our bright, airy factory. Such a refreshing aroma feels just like going into a forest. Located in Wakayama, Nakai Sangyo Co., Ltd. is a comprehensive manufacturer of woodworking products with a specialization in shoji screens. With lots of forest, the Wakayama region has traditionally served as a manufacturer of building fixtures for the greater Kansai area. Since our founding in 1939, Nakai Sangyo Co., Ltd. has manufactured such wooden building fixtures. In recent years, we are also making religious Shinto objects such as offering boxes and tablets for shrines.
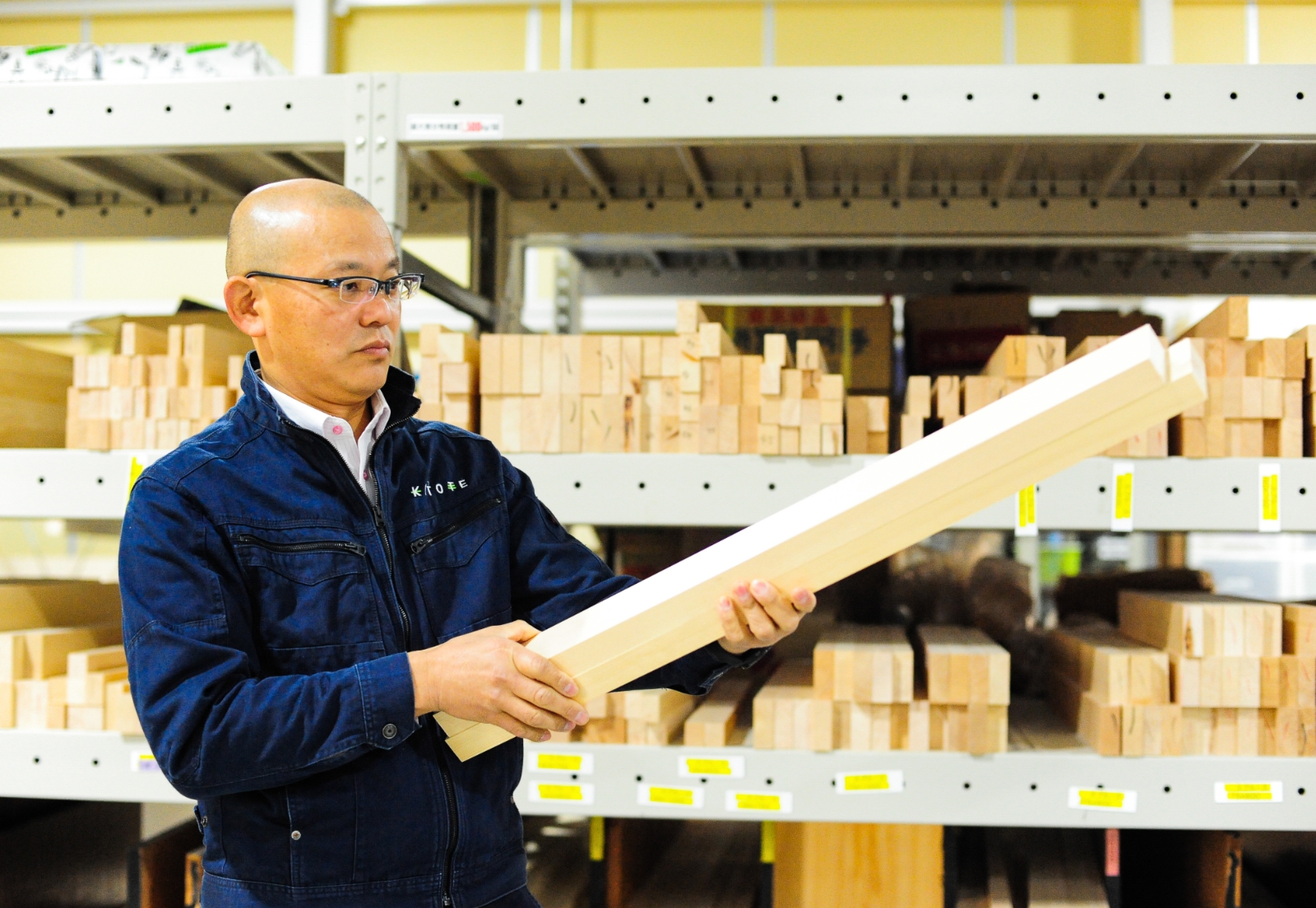
Yoshiaki Ozaki, President/CEO of Nakai Sangyo Co.
Every tree has a unique appearance, with a pleasant texture and beautiful grain. Just like different faces, a tree’s characteristics vary depending on environmental factors such as soil and sunlight. However, many manufacturers in mass production prefer not to use trees. This is because the lack of uniformity in quality makes them difficult to handle. They dislike their individuality.
“I want to further take advantage of wood as a natural resource. The Japanese people have long lived surrounded by trees. Since we Japanese are fond of them, I want more people to experience the real thing” says Nakai Sangyo President and Representative Director Yoshiaki Ozaki. This is what led to the creation of our company’s in-house shoji screen brand KITOTE.
KITOTE uses well-designed shoji screens made from trees to showcase the material’s appeal to the world. Shoji screens are made using a traditional Japanese woodworking technique called kumiko framework. No nails are used. Instead, wooden parts are joined together to create geometric patterns.
While the kumiko framework of traditional shoji screens incorporates vertical and horizontal wooden cross sections, KITOTE’s framework sets itself apart. A double-layer structure is used to allow for vertical and horizontal combinations. A technique called “kiriko” allows the sections to be cut in the middle without fusing to the door frame or crosspiece, creating open space. This adds a modern appearance to traditional Japanese rooms, and adds an elegant and stylish nuance to Western-style rooms. KITOTE is distinguished by its unrestricted designs, which boldly change the impression of shoji screens.
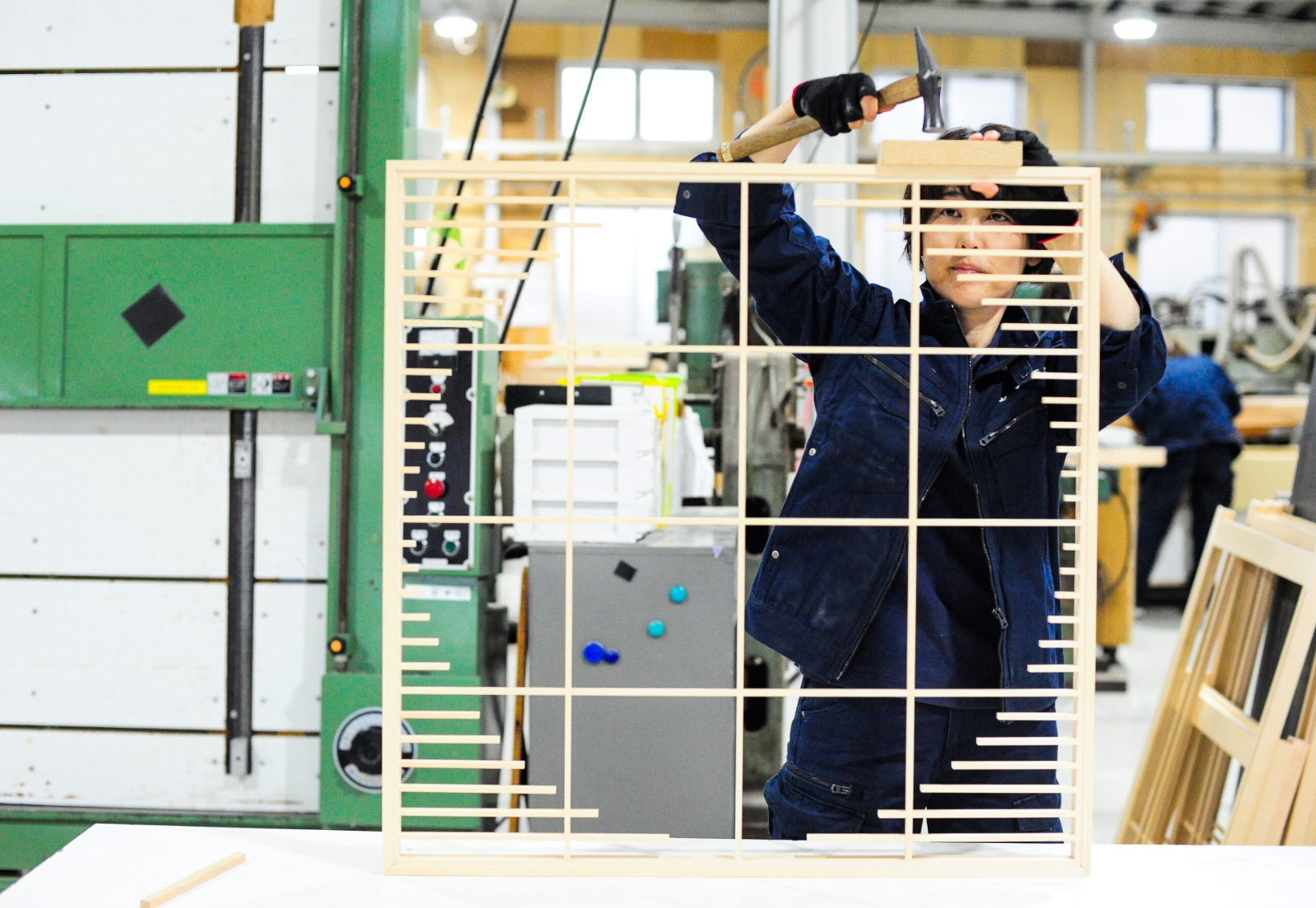
〝KITOTE AIR SHOJI Slim Line Moon〟. The 6mm braided line, which is thinner than the standard 8mm braided line, achieves delicacy.
In completing a piece, one important skill is understanding how the tree will appear. When a tree dries, it loses weight, shrinks, and swells. Its beauty is lost if it is not processed within a precision of 0.1 mm. The level of detail required is cultivated through experience.
Our Craftsmen Understand the Wood, Which Allows Us to Do What We Do
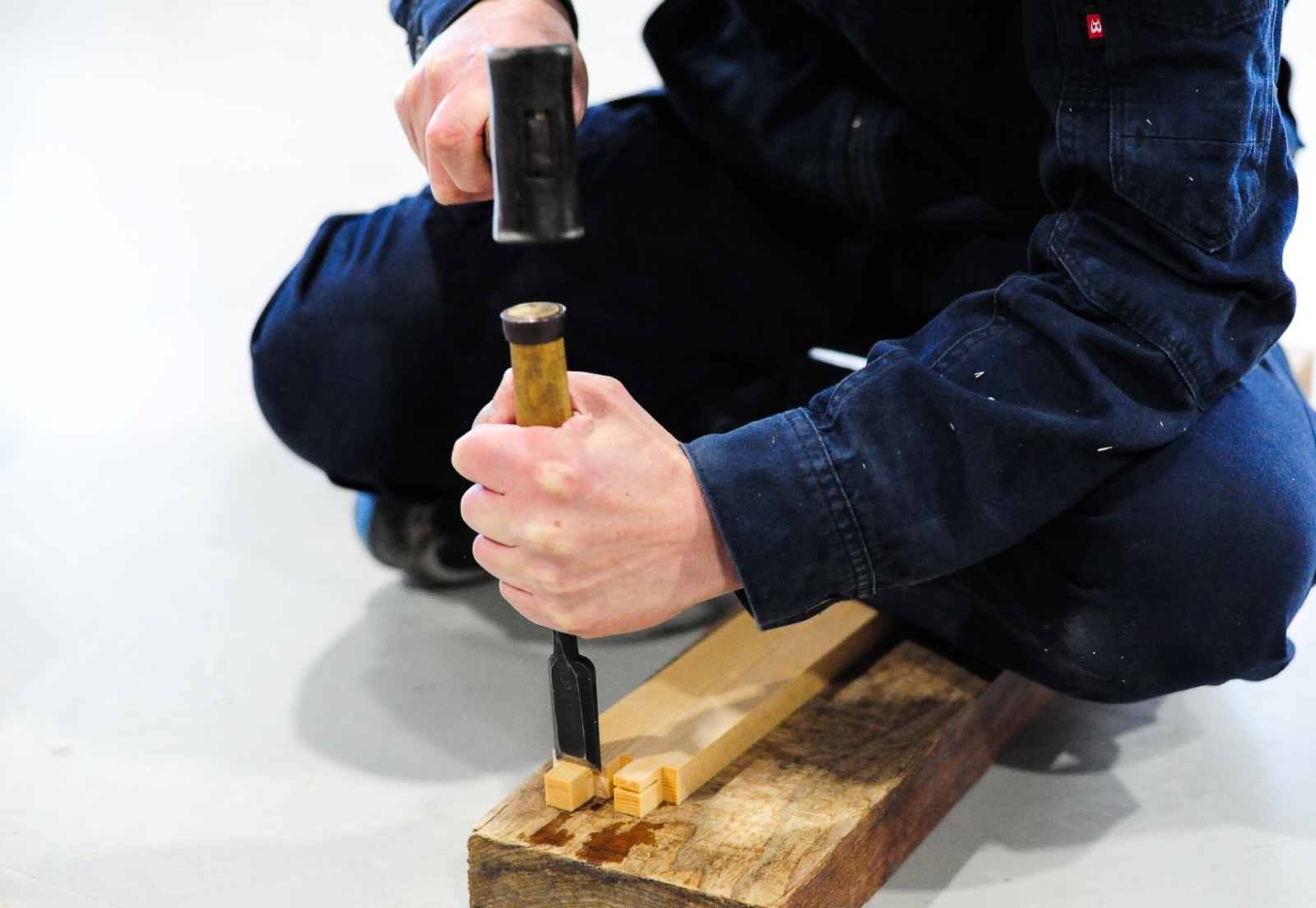
A craftsman handles a chisel to make the “HOZO” for assembling shoji screens.
AIR SHOJI is a new KITOTE product. It all started at Design Inspires Hong Kong 2019. While many people from overseas expressed an interest in the shoji screens’ beauty, they were simultaneously confused by the need for a frame, how it was constructed, and concerned that it would make rooms appear smaller. Shoji screens are used as doors in tatami-floored Japanese rooms, so the presumption is that they are sliding. Outside of Japan, not many countries have a culture of using sliding doors in their homes. KITOTE products were introduced after attracting attention from the editor-in-chief of a Hong Kong-based interior design magazine. Rather than display the products as doors, they were introduced as wall lighting. “I was surprised. The shoji screen appeared as a panel. It was a real eye-opener seeing them used as a decoration,” says Ozaki with a laugh.
Incorporating the feedback from Hong Kong, our company partnered with specialist picture rail company Arakawa & Co., Ltd. to create a hanging panel and a wall panel called AIR SHOJI. The product allows one to enjoy the soft, beautiful look of light passing through the shoji panel. It can be versatilely incorporated into any interior space, whether hung and illuminated at the desired length and size, or fixed to the wall to create geometric art. The moment marked a departure from the fixed concept that shoji screens were sliding doors.
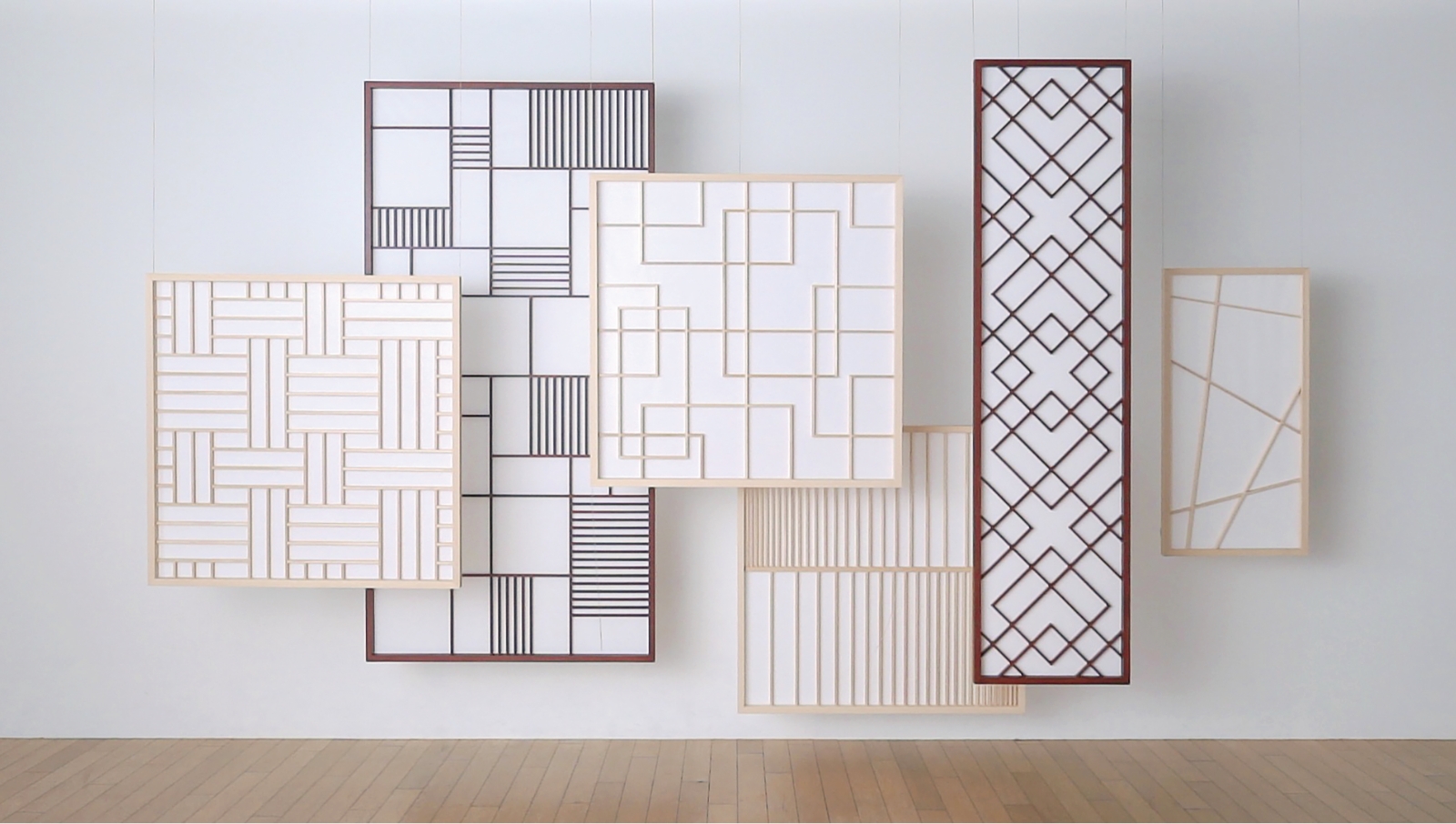
〝AIR SHOJI〟
This experience was essential to us deciding to create one-of-a-kind shoji screens made from trees. Created in 2014, KITOTE’s development process led to major innovations in the factory. At the same time, at Nakai Sangyo, we were facing challenges with how to pass on the technical skills of long-experienced artisans to young people. President Ozaki came to the conclusion that rather than learn through observation, it would be necessary to systematize the process in order to pass down the wood fitting production process to the next generation. Working with Manufacturing Department Chief Akihiro Ueda, they endeavored to create quantified manual of the crafting process.
It took six months to create the manual. Following that, it was decided that machines would be adopted for tasks that could be optimized for efficiency, and that craftsmen would carry out processes that required attention to detail. During this time, the company pushed forward with training of younger craftsmen, and worked to reform conceptions about the production process.
While these reforms saw some internal opposition and created various problems, the resulting achievements led to our company receiving a Good Design Award in 2015 (sponsored by the Japan Institute of Design Promotion). Our small factory is now considered a highly regarded woodworking manufacturer.
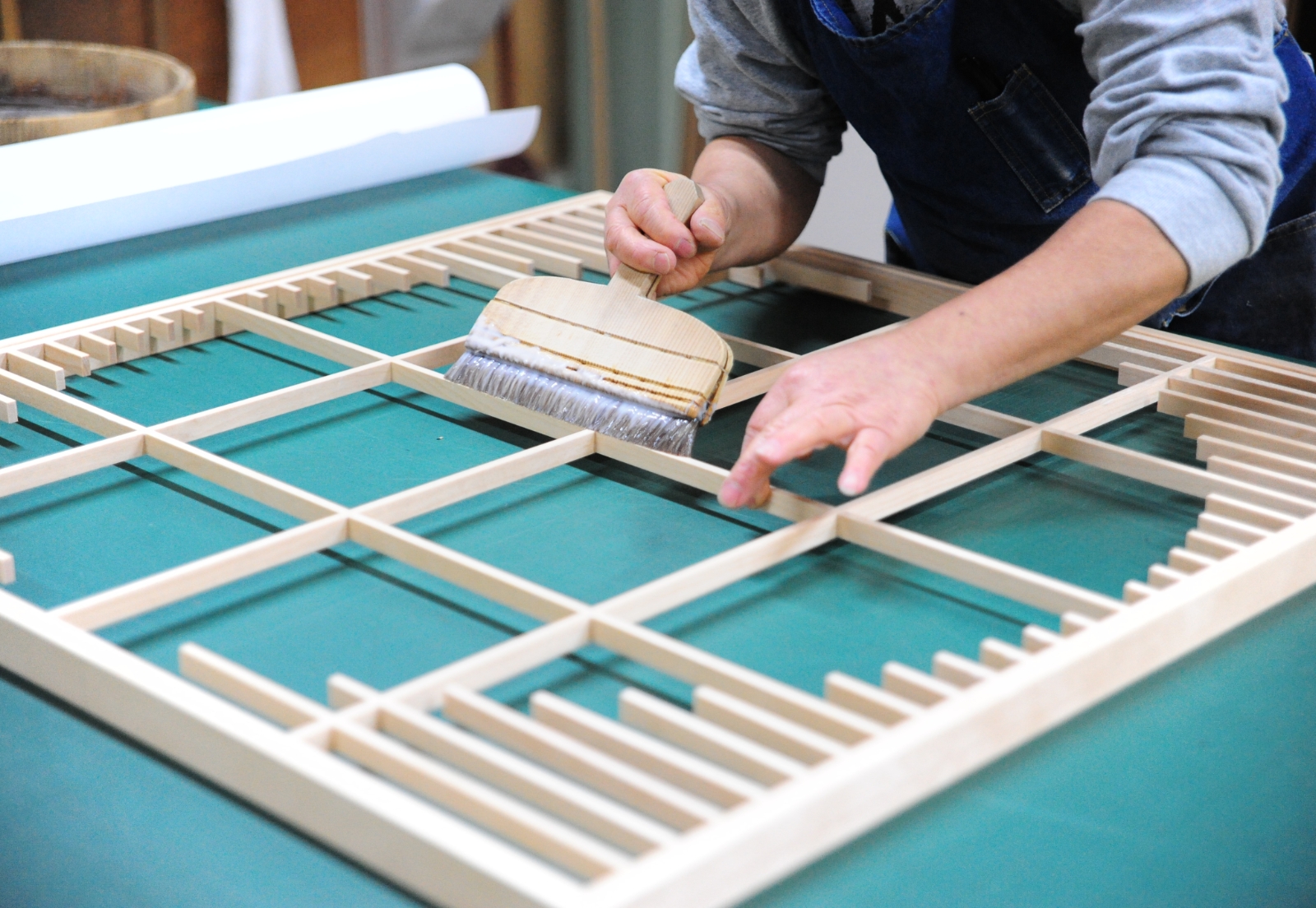
A craftsman applies shoji paper one by one.
We also recently allied with Kidukai no Undo, an organization promoting environmental conservation activities. By proactively using Japan’s trees, the company aims to revitalize the country’s forests. As part of their training, the craftsmen also visit the mountains. Seeing the actual trees they are using has significantly altered their awareness. “We prize the phrase ‘beautification through aging.’ This refers to how objects change for the better over many months and years. By promoting woodworking, I hope to cultivate the prosperous development of both people and trees. I am happy that our products are being used as a step in this process.”
At Nakai Sangyo, we are protecting Japan’s trees and increasingly rare craftsmanship, and we hope to continue doing so well into the future.
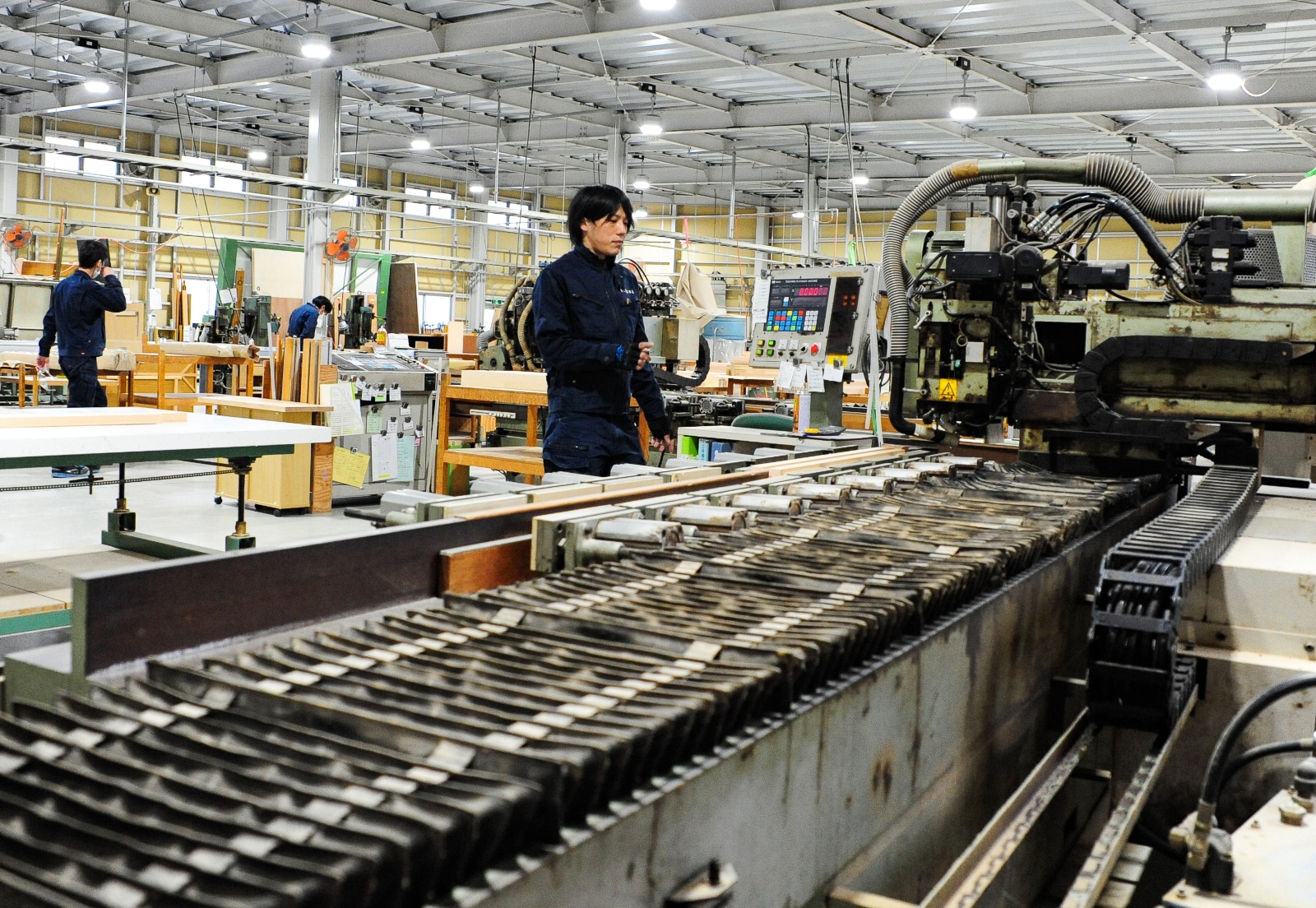
Many young employees are at the forefront of their field by learning manualized master techniques.